By: Metal Culverts, Inc
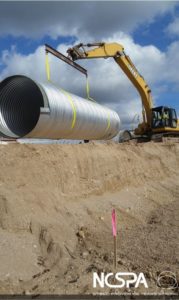
The Lifeblood of the Badger State: Ensuring Wisconsin Water Quality Protection
Wisconsin’s abundant water resources, featuring over 15,000 lakes, proximity to Lakes Michigan and Superior (two of the world’s largest freshwater sources), and 32,000 miles of streams, are essential to the state’s identity and economy. Wisconsinites rely on these waters for drinking, recreation, agriculture, and a vibrant tourism sector. Consequently, maintaining the quality of these invaluable resources is paramount. To that end, robust stormwater management solutions, particularly the implementation of underground corrugated metal detention systems, have become a primary focus for municipalities and state environmental agencies. Strict stormwater regulations are in place to mitigate the effects of urban expansion and ensure ongoing Wisconsin water quality protection.
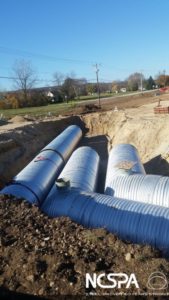
Underground Innovation: Implementing an Underground Corrugated Metal Detention System for Effective Stormwater Management
Plymouth Foam, a designer and manufacturer of foam products for the construction, packaging, display, and OEM markets, recently embarked on an expansion project. This project took place at their Plymouth, Wisconsin facility. Consequently, this expansion necessitated the development of a new stormwater management plan to address the increased runoff.
However, due to the unavailability of additional acreage for an above-ground detention basin, an underground system presented the most economical solution. Nevertheless, a unique challenge arose at this site: an unusually high water table. This factor, therefore, precluded the use of any perforated retention system. Instead, designers selected an underground corrugated metal detention system. This system consisted of 1,242 linear feet of 96-inch 14-gauge Aluminized Type 2 material, fabricated by Metal Culverts Inc. and installed by Wagner Excavating of Sheboygan, Wisconsin.
Moreover, the structure provided approximately 62,500 cubic feet of water storage. By employing below-ground storage, the system was designed large enough to accommodate 2 to 3 feet of permanent water storage at the bottom of the pipe. This allowed for total suspended solids removal. In this way, specialized stormwater management solutions were necessary, particularly for this complex construction project.
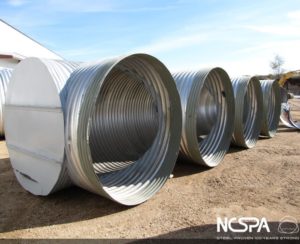
Navigating Construction Challenges: Implementing Effective Construction Site Stormwater Control
Moreover, to compound the challenges at this site, Wagner’s crews had to navigate incoming and outgoing truck traffic servicing the existing facility. This was a critical consideration for effective Construction Site Stormwater Control. According to Wagner project manager Josh Salm, the installation progressed swiftly and was completed in a timely manner. This was achieved without significant disruptions to truck traffic flow. Furthermore, the presence of active truck traffic left minimal space for storing the unconstructed system. Therefore, Wagner collaborated closely with Metal Culverts Inc. to establish a delivery schedule. This schedule prevented “overloading” the busy job site, thereby ensuring that the necessary components arrived on site precisely when needed. This meticulous planning was essential for maintaining proper Construction Site Stormwater Control.
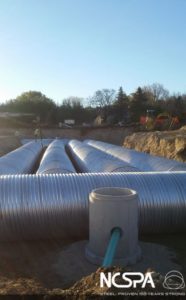
The Versatility of CSP: A Cost-Effective and Customizable Solution for Wisconsin Water Quality Protection
Ultimately, corrugated steel pipe (CSP) provided the ideal solution for a detention system. It was not only cost-effective but also versatile and fully customizable. By utilizing a CSP system in this specific situation, the engineer was able to design a structure that met the owner’s requirements. Additionally, it complied with all applicable city and state code requirements. Therefore, it ensured Wisconsin water quality protection. In summary, providing effective stormwater management solutions, particularly through the use of an underground corrugated metal detention system, and maintaining proper Construction Site Stormwater Control required careful planning. It also required the use of the right materials and methods.
Related Stories
Stormwater Retention System: Sustainably Transforming Beacon Bluff
ViaCon Steel Culverts: Saving the Day on Turkey’s Balıkesir-Manisa Road
Project Spotlight: Tractor Supply Sand Filters