First & Main Storm Water Management System Optimization Design/Build Venture Revives Retail Development – Blacksburg, Virginia
With the onslaught of new water quality devices, the ever-changing pollutant removal parameters, and the growing list of acronyms to memorize (BMP, LID, LEED, et al.), today’s civil and site engineers face no small challenge in staying on top of their game. Coupled with the economic crunch and the limited resources available to developers, the demands placed upon design are more critical than ever with no room for taboo terms such as over-budget and over-design. What many fail to acknowledge is that achieving optimization in storm water management is not what it may seem, and sometimes providing more is less. These truths are best illustrated by a recent development in Blacksburg, VA commonly known as First & Main, a high-profile retail development politicized on a number of fronts, not the least of which was storm water management.
Hydrologically, the site presented the types of challenges that could easily make or break the development. Firstly, large amounts of off-site drainage traversed the 27 acre tract, amounting to 200 cfs for the 25-yr event. Secondly, a portion of the pre-developed property was naturally detaining this off-site drainage and was configured as regional storm water detention. Thirdly, water quality measures upstream of the development were in place, and in effect the off-site drainage was already being treated to the satisfaction of the regulating agency. Thus the objective became storing both the off-site and on-site drainage, treating only the on-site portion of this mixed flow, all in the same “natural” detaining area as to mimic pre-development hydrology.
The initial storm water management design was cost prohibitive, with installation and material costs totaling around $3M. At that point the developer did two things: (1) commissioned Balzer & Associates to explore alternate methods of calculating storm runoff volumes, peak discharge rates, et al., and (2) asked Lane Enterprises to provide design/build options for the storm water management system. The combination proved effective, lowering related costs to around $1M.
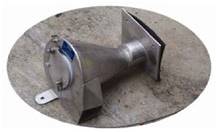
Balzer & Associates effectively eliminated 40% of the storm water to manage by liberating themselves from the simplified procedures of TR-55, and opting for the tried-and-true Rational Method. It was then left to Lane Enterprises to optimize how the resultant flow quantities would be managed.
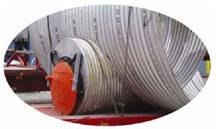
A joint venture between Lane Enterprises and Hughes Associates Architects was ultimately successful in providing the design/build option the developer needed. Lane began by upsizing the storm water management system (SWMS) to 12-ft diameter corrugated metal pipe. The increase allowed a smaller footprint, less excavation in an area underlain by rock, and correspondingly less material to haul from the site.
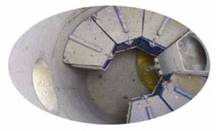
The SWMS offered a number of features that all played a part in system optimization. All in all there were twelve nodes configured into the HydroCAD modeling software. The critical node was the head building chamber, a smaller compartment designed to fill rapidly before cresting weirs and filling the SWMS proper. This feature enabled the full orifice head (in this same chamber) to be realized at the beginning of the storm event, eliminating the need for the entire system to fill before achieving the maximum allowable discharge, and correspondingly eliminating unnecessary storage volume.
In the same manner and with similar effects, water that crested the weirs was directed through a Reg-U-Flo® Vortex Valve, a device designed to achieve maximum discharge rate at the lower pressure heads while maintaining that same discharge rate at the higher heads via a restrictive vortex created through the outlet of the device.
As long as the main dewatering line was not surcharged a secondary outlet was available through the operation of a backflow preventer (i.e. check valve). This device in full swing revealed another orifice outlet to mobilize additional allowable discharge which also contributed towards minimizing storage requirements.
Another feature that contributed toward the minimization of required storage was the ability to utilize 6″ of the pipe bedding material for storing the water quality volume (WQv). This was accomplished by adding a full run of 12-ft diameter perforated pipe into the SWMS, in addition to roughly 360-ft of Lane’s 6″ HDPE under-drain to intercept and outlet the WQv through the Up-Flo™ Filter.
Countering much of the design work at this point the system storage was actually increased to accommodate a more restrictive filtering device. This move enabled the removal of a sizeable and costly ($250k) concrete vault containing nearly 80 filter cartridges, and made way for a more reasonable ($40k) standard 4-ft diameter structure with only six filter cartridges. An Up-Flo™ Filter with capacity to pass 0.33 cfs was all that was needed for the value engineering judgment. Thus, sometimes more is less.